In this opportunity I will share about the experience automating part of an industrial process a few months ago and use industrial Panasonic brand equipment, since I consider that I know this brand well in PDAControl we have compiled a great amount of tests and integrations with hardware such as Arduino, ESP8266, ESP32 and other IoT platforms.
There are other “PLC” controllers and “HMI” screens of great renown, such as Allen Bradley or Siemens, Omrom, Mitsubishi, Sneider, Opto22 and Festo, of course Panasonic at the automation level of machines is a mixture of simplicity, practicality and robustness , technically I learned it very well and I liked it.
In detail…
A few months ago I contacted a colleague who had a project, about some grain packing machines and they were deciding whether to buy new machinery or re-empower the controllers and screens the old machines.
Accept re-empower a machine and place the condition of automating with Panasonic, consider it more a personal and professional challenge.
The following video is a sample of the automation process performed to enter context, this is the introduction: Automation with Panasonic.
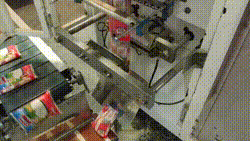
The intention of this guide is to indicate some suggestions and recommendations that I personally consider important for automation, be it at an industrial level mainly or at a manufacturer level and, of course, share the experience.
The following video is a sample of the automation process performed to enter context, this is the introduction.
Complete Video:
1. Initial Information Survey
First of all, a large survey of detailed information can be simply a series of visits.
- Blueprints.
- Manuals
- Documentation.
- Survey of signals, variables, sensors and actuators.
- Analyze the variables that affect the process.
- Listen to process owners, operators, maintenance team.
Technically, in my case they required an identical copy of another machine, as well as an additional parametrizable and add OEE indicators and faults.
We only had a user manual for the original INDUMAK machine, where they literally indicated how the machine worked, that manual was very helpful.
2. Measure your capacity and availability
This is an analysis of your scope or your team, referring to measuring the difficulty of the process and if you have the knowledge and skills to do it.
I have seen very complicated processes and I have determined not to accept them, due to the following factors:
- They take a long time in implementation and testing, the client will not pay for this development time.
- There are applications that involve competences or skills in certain areas that I am not aware of, such as welding and mechanics.
- Processes, systems or machines very complex or specialized in which there are machines manufactured for these specific functions, no adaptation or similar implementation will match them.
The machine in my case to the naked eye appears to be complicated and complex, apart I trusted in my ability and had experience and I greatly influenced the next step Number 3 to accept the project and had already determined the most complex to perform a dynamic routine of synchronization of actuators , the synchronization and time adjustments was what took 5 days, since it also involved a thermal seal and cut that should be precise.
The following video is a sample of the automation process performed to enter context, this is the introduction: Automation with Panasonic.
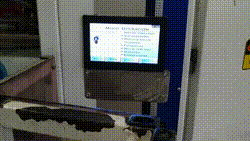
3. Select the Hardware & Software
For hardware selection I recommend taking into account the following:
- Having previous experience with the selected hardware, this will save time in development and implementation.
- In case of not having experience and using new software / hardware, document and search for case and implementations in the network.
- Technical support by the provider.
- Spare parts and guarantees.
- Analyze and determine the scope of the project so as not to overspend unnecesary hardware expenses. Example: IO modules and expansions.
- It also analyzes if in the future the project could expand, grow or integrate with other hardware, software.
- Software license costs.
In the case of the automation that was carried out, regarding the packaging machine, the original process had a PLC Micrologix 1200, although I know and programmed Allen Bradley, I have more experience and malleability in Panasonic Hardware.
The following video is a sample of the automation process performed to enter context, this is the introduction: Automation with Panasonic.
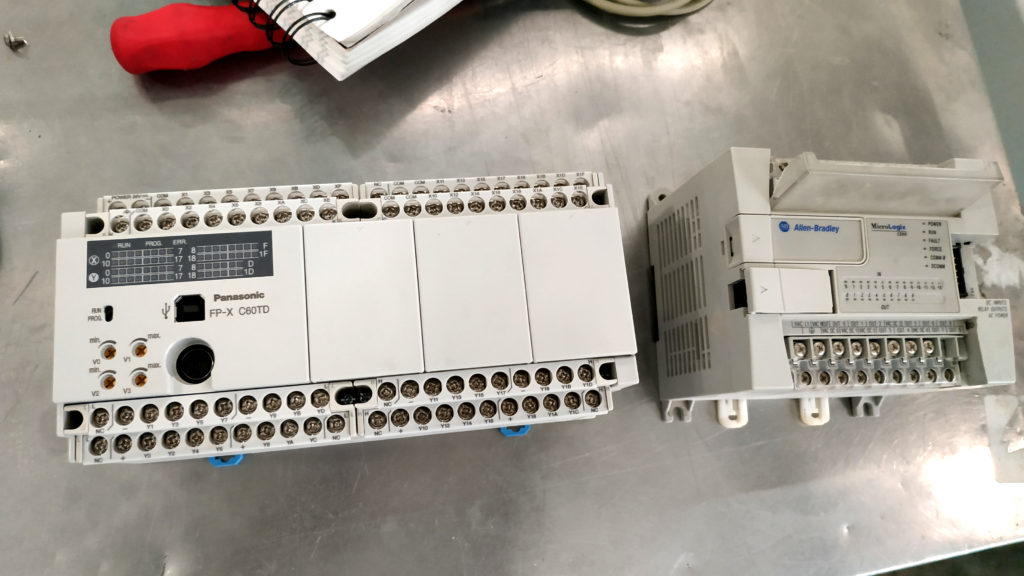
PLC FP-X C60 TD
This is the PLC FPX C160 TD from Panasonic, has 32 digital inputs and 28 transistor outputs, 4 potentiometers and Toolport port for programming and / or communication with HMI and a USB port type B for programming, if more inputs are required I / O expansions can be added and finally 24VDC is fed.
Programming Software FP-WIN Pro which I personally prefer has several languages to program or FP-WIN GR for programming only in LADDER language
Recommended: Full information Panasonic family Fpx.
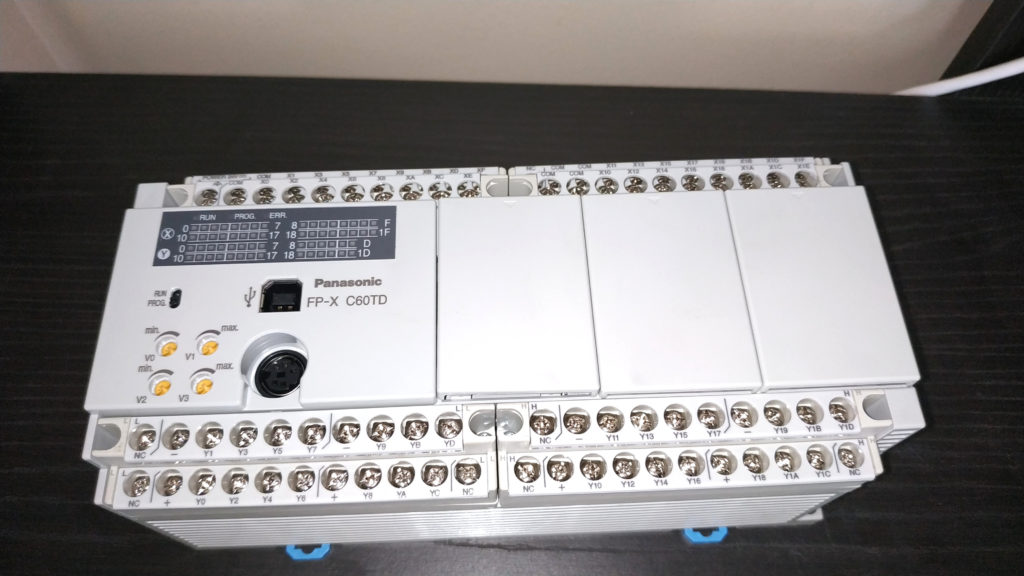
HMI GT707 with 7″
This screen is the Panasonic GT707, has 7 inches that color, touch an RS232 serial port for serial communication with the PLC, SD card slot for recording and storage of data and recipes, mini-usb port for programming.
GTWIN Programming Software in the latest versions, maximum demo version 10 screens available in Panasonic web site.
Recommended: Complete information HMI GT707.
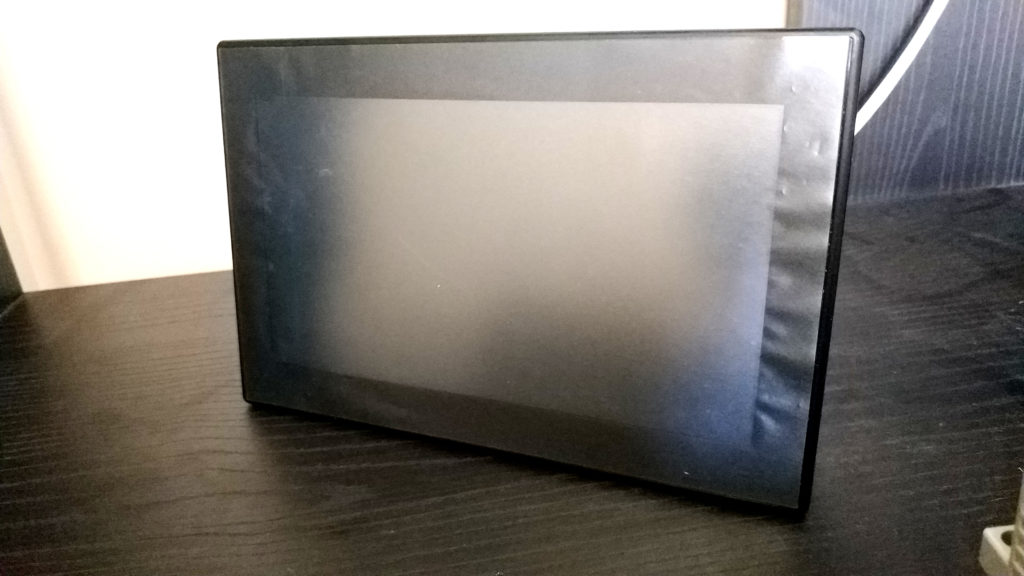
4. Estimate times
A part should be done in a group, if several people involved in several areas project, for example: electrical equipment, team of mechanics, team of programmers.
A previous chronogram is always determined, for greater accuracy in time to make this schedule in conjunction with the client and suppliers.
In terms of determining the development time, do not underestimate the complexity of a process, no matter how simple an application, it requires robustness and security.

In the case of the previous project, the client requested 10 days to automate the machine, technically program the PLC and the HMI, the client considered that it was only to change them, and already, similar to how to change a relay “hahahaha” , they also had the production lost against, that is, they were not producing so they needed the machine as soon as possible.
Considering that the zero program should be done only based on the operation of another similar machine, 15-20 days were determined in programming and implementation and an additional 10 days of testing time.
Fortunately we took a total of 25 days, 15 days in implementation and 10 days net.
The following video is a sample of the automation process performed to enter context, this is the introduction: Automation with Panasonic.
4. Modeling Programming Algorithm
Based on the requirements and signals of the process, make a sketch on paper, analyzing or simplifying the process.
I personally before programming or generating code specifically, I take some time with paper in hand fully understanding the sequence of the process and how it should and / or should work the final application.
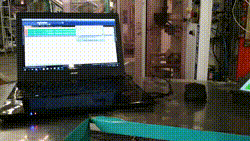
The flow chart is a highly recommended tool for analyzing sequences.
After having relatively clear how it should work, to program ..
I usually start by creating very simple sequences step by step, programming and testing small parts that is my philosophy. usually in some cases they try to do a whole gigantic program and in the end prove, few cases in which prefect works, in the case of PLC or hardware that intervenes with physical variables of the real world, unlike implementations in other fields or languages of programming, example: making a web application in javascript, HTML in general are environments under control, it will not have condensation that affects a cylinder or failure in a thermal resistance.
Important: in an industrial process, not only risk raw material or machinery also risk lives, always determined:
- Emergency stops (local and remote)
- Initial process conditions, before starting.
- Fault conditions, eg broken or failed sensors.
- Restart conditions in case of power failure.
- Menus approves of Operator errors.
- among other possibilities.
Recreate process or simulate process
Usually we do not have the equipment or infrastructure to completely recreate a process, my suggestion is to simulate, in my case I did not have a machine available, system with pneumatic, mechanical, electrical actuators, similar to the real machine.
Technically I made a very generic code of the process and when I arrived at the plant I made the real code, since it suffered several changes before the final version, I would say that the program was done in the plant.

Conclusions
For a long time, I have not accepted to carry out automation projects more specifically control projects in general, since control takes time and influences many risks, the case of the grain packing station intervenes;
- Temperature control for bag sealing,
- Precision in thermal sealing and cutting.
- Synchronization in product dosing system.
- Configurable system of 50 configurable recipes.
- Parameters of Quality of the company to accept the bags packed
In the process they intervene:
- Electrical system: Contactors, Mechanical relays, Transformers, Solid state relays and motors.
- Pneumatic system: Solenoid valves, double and single effect cylinders.
- Mechanical systems: sprocket and reduction boxes for displacement of cylinders.
I prefer by experience to select projects that require only monitoring, counting and measurement, projects that are not high risk or directly affect a process.
Determine to automate this machine to demonstrate other products (PLC) different from those generally used and that was in the scope to automate the process and improve it.
Well that alone is my opinion and my experience, I hope it can be a contribution only some suggestions and recommendations, not taking them as rules is only partly my method and it has worked for me.